Modes of dispersion
Dispersion is the enemy of high resolution. It is also referred to as band spreading or peak broadening. Dispersion is a compound parameter combining contributions from modes of flow, modes of mass transport, mobile phase viscosity, solute size, and friction. Since different chromatographic architectures are associated with distinctive modes of flow and mass transport, the degrees of dispersion they impose are also distinctive.
Studies with monoliths show very low Reynold’s numbers that indicate flow is almost exclusively laminar (devoid of vortexes) (Image 1). With laminar flow key solute dispersion comes from laminar dispersion. As flow velocity approaches zero at surfaces of channels due to friction, strata (lamina) further from the surface flows faster because friction is reduced, causing onset of laminar dispersion (Image 2). Laminar dispersion increases with increasing flow rate for all chromatography media, but its effects are dwarfed by the loss of diffusive mass transfer efficiency and dispersion caused by eddy vortexes in porous particles.
Viscosity increases frictional drag at media surfaces, thus increasing laminar dispersion in all chromatography media. Viscosity heavily compounds dispersion in porous particle columns because it decreases efficiency of the primary mode of mass transport: diffusion. Diffusive efficiency is inversely proportional to viscosity; doubling viscosity decreases diffusivity by half. Viscosity, however, does not affect the efficiency of convective mass transport, dominant mass transport mode in monoliths.
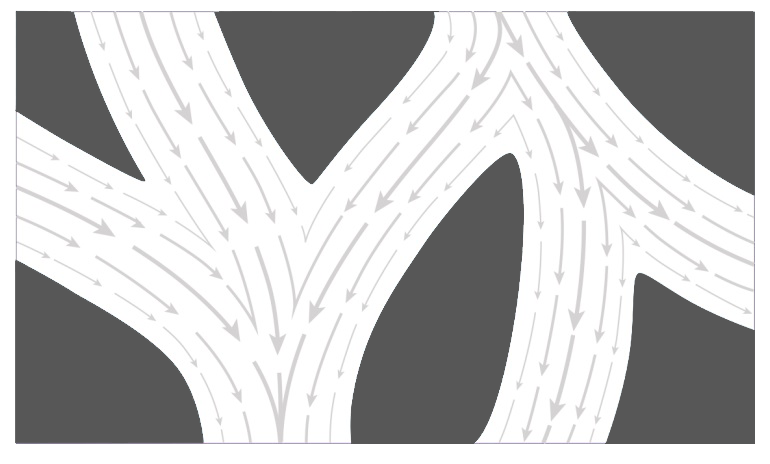
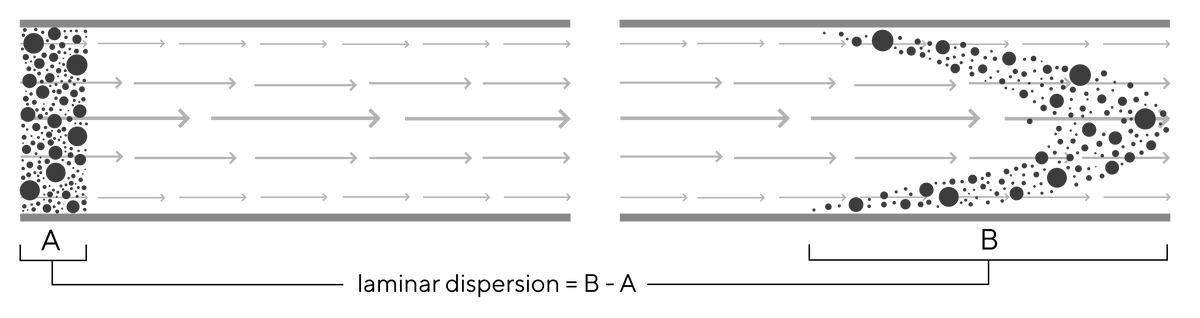
Fluid transport across irregular surfaces produces microturbulence, which affects different media in different ways. Surface roughness creates vortexes which cause some of the solute front to lag behind the main body (Image 3). It compounds the effects of laminar dispersion and contributes to peak tailing, for all media. Surface microturbulence imposes a second burden on particles that is much more serious. It creates a barrier film that hinders solute diffusion into and out of the pores. Film dispersion itself is independent of flow rate but it compounds loss of diffusive mass transfer efficiency in direct proportion to flow.
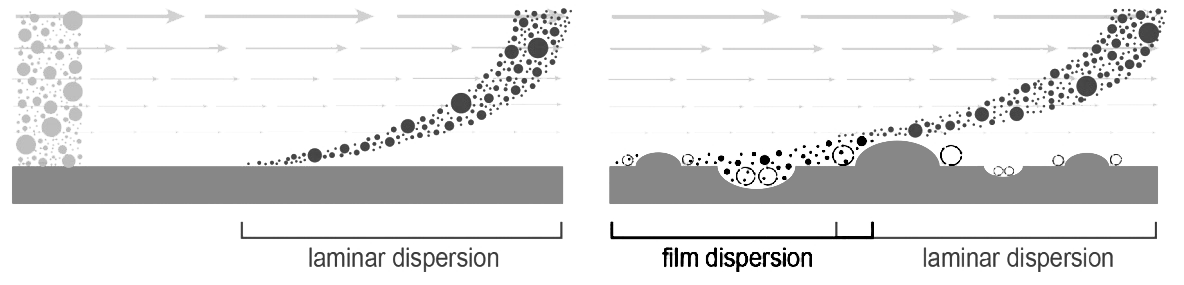
Main constraint of particle packed columns is the loss of diffusive mass transfer efficiency. Solute size and flow rate have profound impact on the efficiency of diffusive mass transfer. Larger size means slower diffusion constants and higher flow rates mean less time to reach equilibrium. These factors force the zone of best performance to a narrower range of lower flow rates with increasing solute size, imposing serious limitations on the downstream process design.
There are five modes of dispersion in columns packed with porous particles: axial diffusion, laminar dispersion, film dispersion, inefficiency of diffusive mass transfer and eddy dispersion. As a source of dispersion, eddy dispersion is second only to loss of diffusive efficiency. Irregular cavities in flow streams of particle based columns create large vortexes (known in chromatography as eddies), which cause turbulent flow (opposed to the laminar one) (Image 4). Dispersion occurs because solutes that become included in eddies remain there for extended periods compared to bulk flow along the primary flow axis. Vortexes appear in all void compartments and total eddy dispersion is proportional to average void compartment size. Larger and/or more heterogeneous particles create larger void compartments that generate more dispersion. Solute residence time within an eddy is proportional to eddy size and inversely proportional to the rate of eddy circulation. The positions of eddies within a void compartment remain constant regardless of flow rate, they just spin faster or slower. Eddy dispersion is independent of flow rate because the rate of solute clearance from eddies is directly proportional to flow rate.
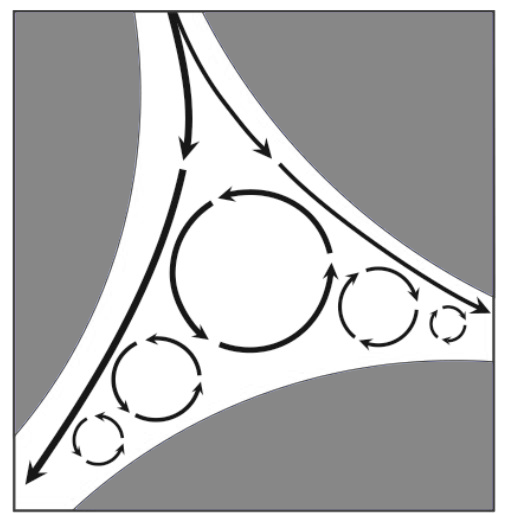
Cumulative dispersion in porous particle columns versus monoliths
Cumulative dispersion in porous particle columns is greater than in monoliths because there are more sources of dispersion, the biggest being diffusive mass transfer. Monolith architecture and convective mass transfer suspend the major sources of dispersion and give better resolution for all solute sizes at all flow rates.